螺纹刀片选用
为了使您有良好的加工品质,在选购和使用时请考虑以下几点:
1、根据加工内、外螺纹、螺纹旋向及工件螺距、牙数/英吋,按我们提供的“切削外(内)螺纹用刀片”表选择 合适型号的螺纹刀片(样本),并请与我们的销售人员商量,根据被加工零件的材料,选择最适合您使用的刀片牌号。
2、根据您所采用的车床的型号,加工方式及已选用的刀片型号来选择适当的刀杆型号。
3、刀垫选择:螺纹的螺旋升角必须和刀片的倾斜角一致,尽可能避免后刀面一侧的不利磨损,致使刀具寿短。我们在制造螺纹刀杆时已经将刃倾角(λ)值设计为1°
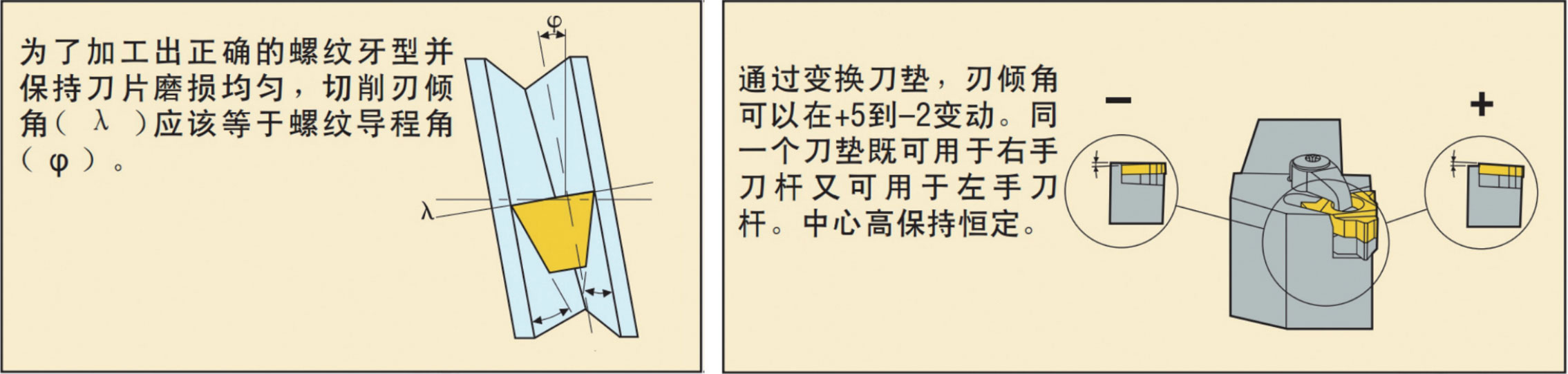
4、切削速度的选择:
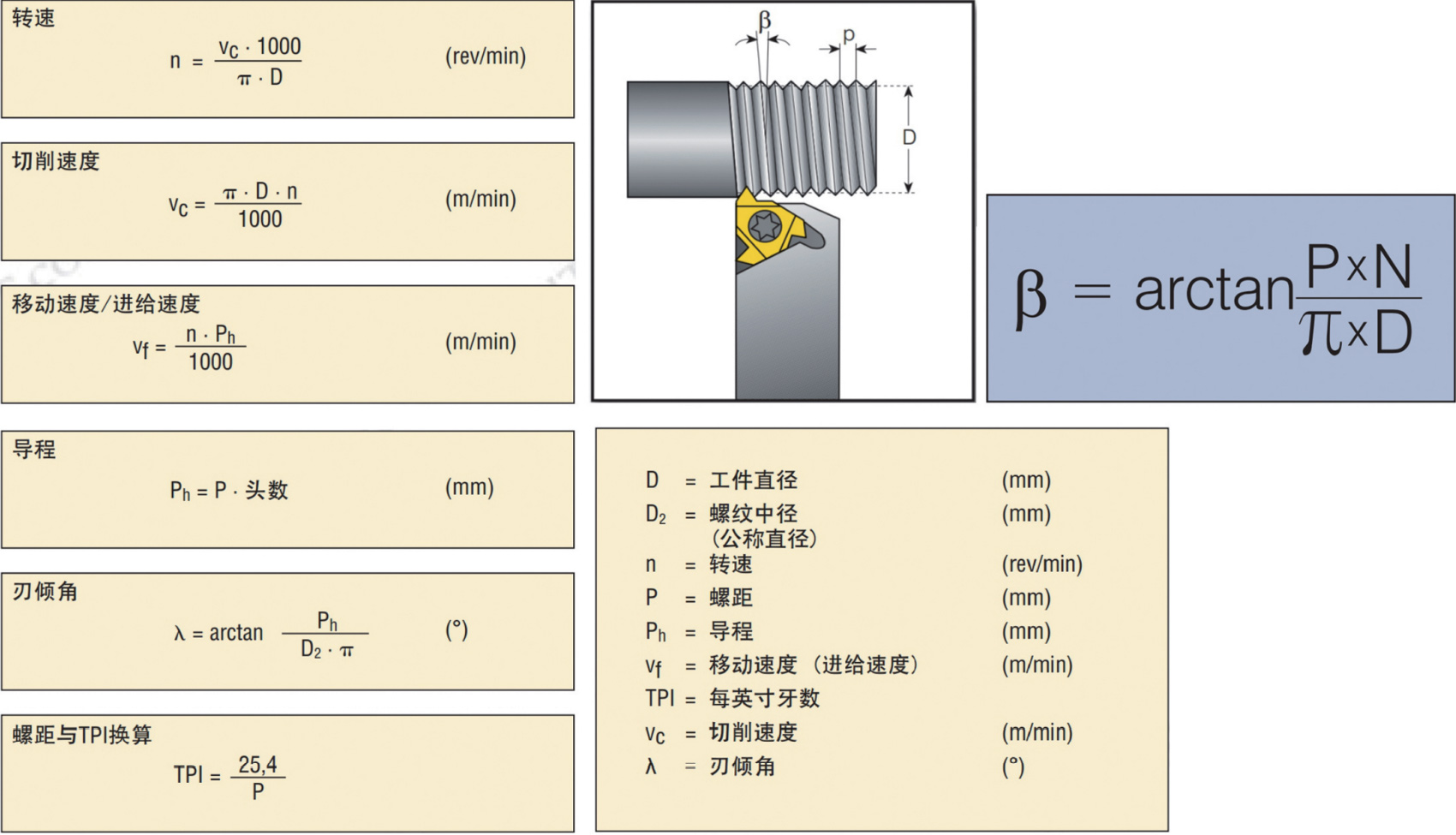
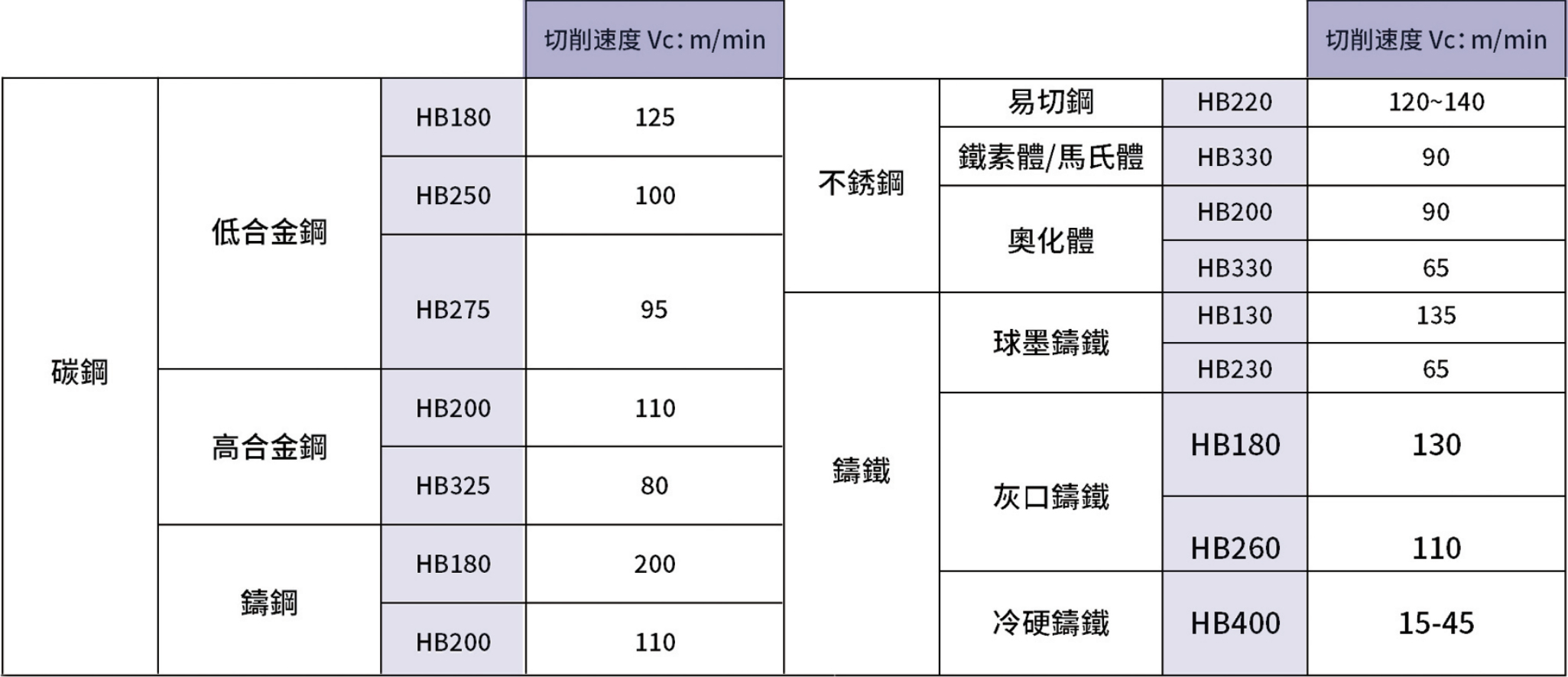
对于不锈钢的螺纹切削,最重要的是切削速度VC要足够高,以避免“积屑瘤”现象。
为了提高小刀尖角刀片的寿命,比如NPT螺纹,可先用较大刀尖角刀片先加工一次,或将切削参数相应改变(增加切削次数)。
5、进刀方式选择
- 径向进刀:通常车削螺纹时,应先选择径向进刀的方式进行,此法操作筒单,且对有加工硬化倾向材料如 奥氏体不锈钢材料的首选。当加工大螺距时,易产生振动,可改为侧向进刀法或互动式进刀方法。
- 侧向进刀法:易于对切屑流向的控制,便于切屑的排出及减轻车削螺纹时的振动,螺纹的表面粗糙度良好。为了在侧向进刀时保持刀片齿形仍能获得均匀的磨损,对600公制螺纹采用在径向切深AP的同时,在轴向进给 1/2 AP的方法获得:
- 互动式进刀:大螺距粗牙螺纹首选,可明显减少刀片磨损,提高刀具寿命,易产生断屑问题,适合CNC数 控机床上使用。
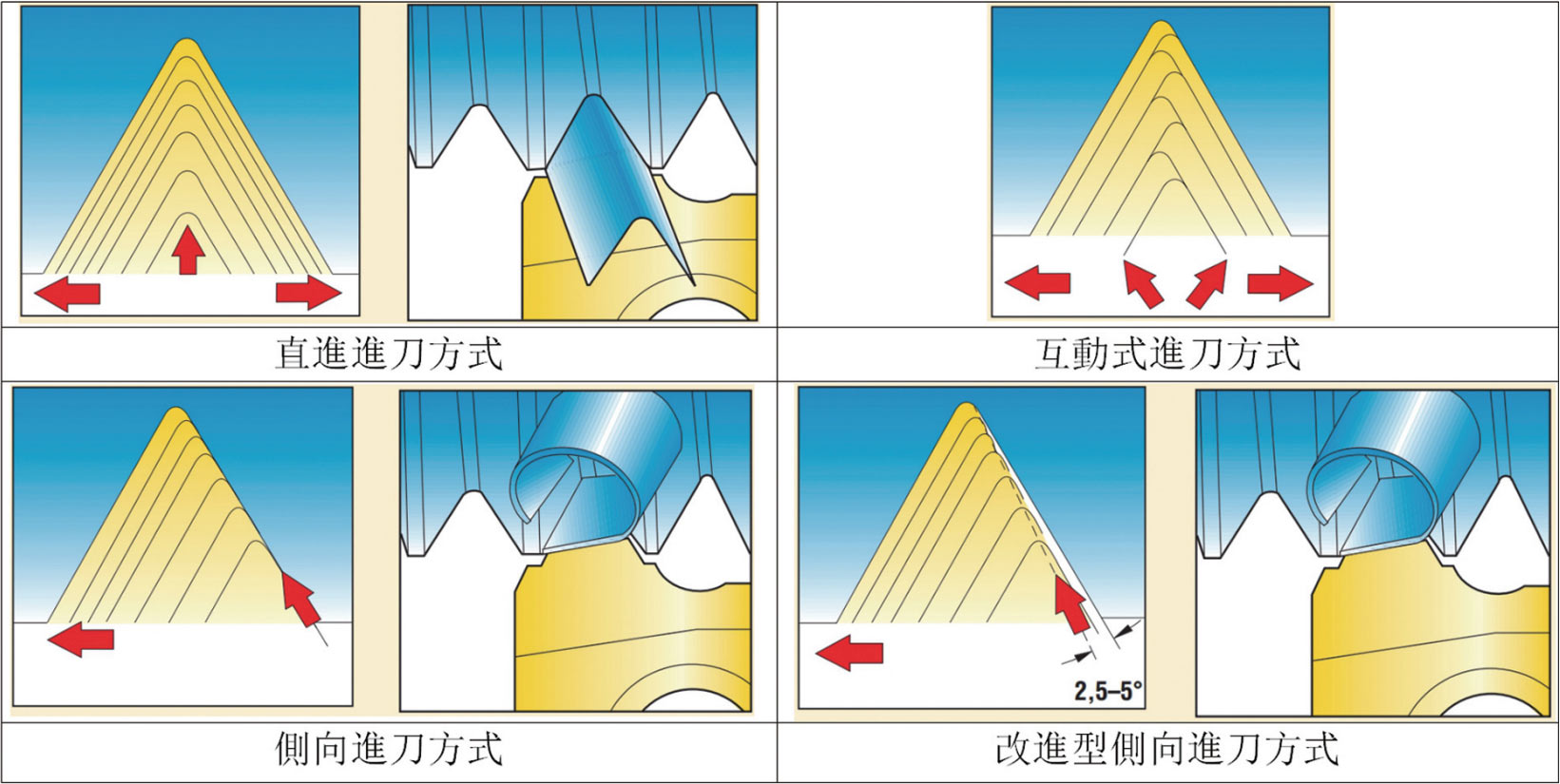
6、步数与进刀深度
由于相对较脆的切削刃,螺纹不能一次切削完成。总的切削深度要分几步完成,每一步都需保持相近的切削力 (相同的切削面积)。
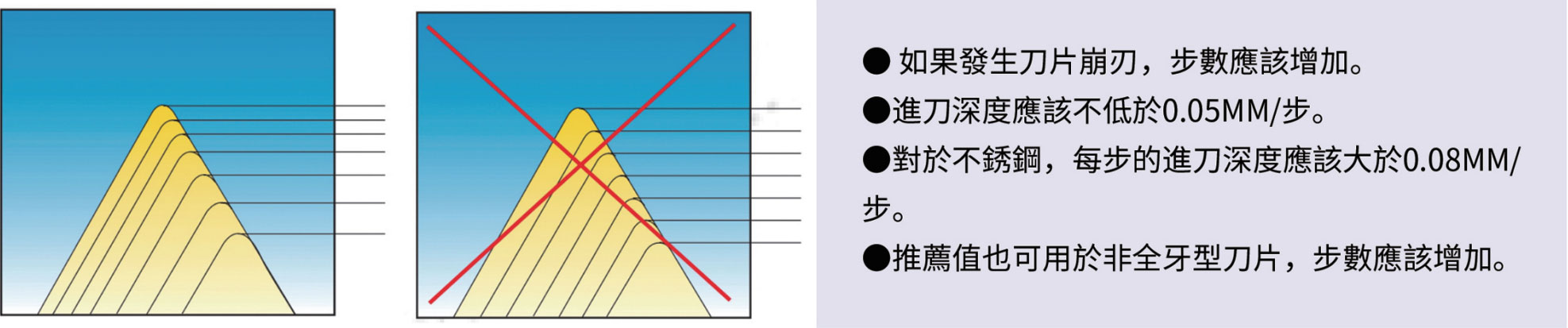
7、进刀量推荐值
在大多数CNC机床上,螺纹加工的一个周期中,(如螺纹加工的固定回圈)总的螺纹深度和第一刀或最后一 刀的切深AP值应给出而在第一次进刀时采用最大的进刀深度(刀尖圆弧半径的1.5〜2倍),随后的进刀深度应逐 渐减小。最后一刀的进刀深度应不小于0.05MM的单边进刀量,否则易造成刀尖的磨损和工件齿面光洁度较差。
在目前的数控机床中,螺纹切削(固定回圈)有两种加工方法:
- 径向进刀法均采用G32方式;(G33、G34、G35);
- 侧向进刀法较多采用G76方式;
由于切削方法不同,编程方法不同,造成的加工误差不同。
两种加工方式的编程指令。
(A) G32X (U) ---Z (W) ---F------;
G32编程:切削深度分配方式一般为常量值,双刃切削,每次的切削深度AP编程人员给出。
径向进刀法由于双侧刃同时工作,切削刀较大,而且排屑困难。因此在切削时,两切削刃容易磨损。在切削螺距较大的螺纹时,由于切削深度较大,刀刃磨损较快,从而造成螺纹中径产生误差。由于其加工的牙形精度较高,多用于小螺距螺纹加工中,注意一点的是,刃口容易磨损,因此加工中要做到勤测量。
(B) G76P (M) ® (2) Q (ADMIN) R(D);
G76X (U) Z (W) R ( ) Q ( ) F ( );
G76编程:切削深度分配方式为递减式,其切削为单刃切削,其切削深度由控制系统自动计算给出。
G76侧向进刀法,由于为单侧刃加工,加工刃容易损坏和磨损,使加工的螺纹表面不直,刀尖角发生变化, 而造成牙形精度降低。同时其为单刃切削,刀具负载较小,排屑容易,及减轻车削时振动。此种方法一般适用于 大螺距螺纹加工。在加工较高精度螺纹时,建议采用“双刀”切削,即是先按G76方法时行粗加工,G32方法进行精加工。注意一点的是刀具起始点要准确定位一致,否则易造成乱扣。